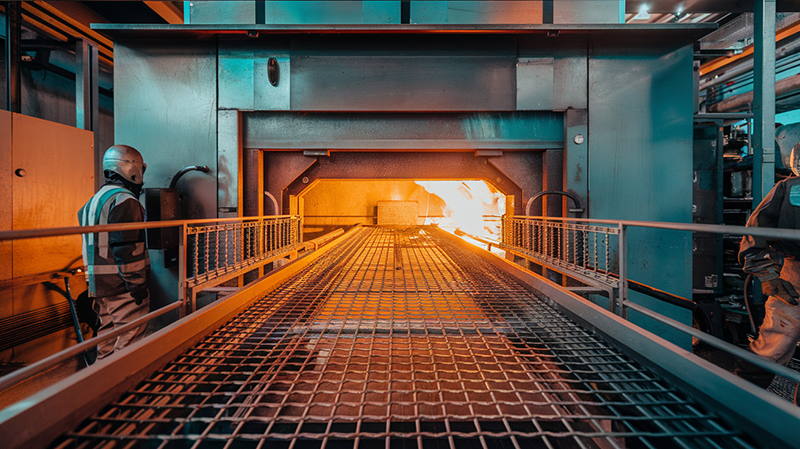
In the demanding world of industrial furnace operations, where extreme temperatures are a daily challenge, high-temperature stainless steel wire mesh plays a crucial role in ensuring efficient and reliable performance. This specialized material combines exceptional heat resistance with durability, making it indispensable for various high-temperature applications.
Superior Heat Resistance Properties
Temperature Capabilities
• Continuous operation up to 1100°C (2012°F)
• Peak temperature tolerance up to 1200°C (2192°F)
• Maintains structural integrity under thermal cycling
• Excellent dimensional stability at high temperatures
Material Performance
1. Thermal Stability Low thermal expansion
a. Resistance to thermal shock
b. Consistent performance under temperature fluctuations
c. Extended service life in high-heat environments
2. Structural Integrity High tensile strength at elevated temperatures
a. Excellent creep resistance
b. Superior fatigue resistance
c. Maintains mesh geometry under stress
Applications in Industrial Furnaces
Heat Treatment Processes
• Annealing operations
• Carburizing treatments
• Quenching processes
• Tempering applications
Furnace Components
• Conveyor belts
• Filter screens
• Support structures
• Heat shields
Technical Specifications
Mesh Characteristics
• Wire diameter: 0.025mm to 2.0mm
• Mesh count: 2 to 400 per inch
• Open area: 20% to 70%
• Custom weave patterns available
Material Grades
• Grade 310/310S for extreme temperatures
• Grade 330 for aggressive environments
• Inconel alloys for specialized applications
• Custom alloy options available
Case Studies
Heat Treatment Facility Success
A major heat treatment facility increased operational efficiency by 35% after implementing high-temperature mesh conveyor belts, with significantly reduced maintenance downtime.
Ceramic Manufacturing Achievement
Implementation of custom-designed high-temperature mesh supports resulted in a 40% improvement in product quality and reduced energy consumption.
Design Considerations
Installation Requirements
• Proper tension control
• Expansion allowance
• Support structure design
• Temperature zone considerations
Performance Optimization
• Air flow patterns
• Load distribution
• Temperature uniformity
• Maintenance accessibility
Quality Assurance
Testing Procedures
• Temperature resistance verification
• Mechanical property testing
• Dimensional stability checks
• Material composition analysis
Certification Standards
• ISO 9001:2015 compliance
• Industry-specific certifications
• Material traceability
• Performance documentation
Cost-Benefit Analysis
Operational Benefits
• Reduced maintenance frequency
• Extended service life
• Improved process efficiency
• Enhanced product quality
Long-term Value
• Energy efficiency gains
• Reduced replacement costs
• Increased productivity
• Lower operational expenses
Future Developments
Emerging Technologies
• Advanced alloy development
• Improved weave patterns
• Smart monitoring integration
• Enhanced surface treatments
Industry Trends
• Higher temperature requirements
• Energy efficiency focus
• Automated process control
• Sustainable operations
Conclusion
High-temperature stainless steel wire mesh continues to be a cornerstone of industrial furnace operations, providing reliable performance under extreme conditions. As industry demands evolve, this versatile material remains at the forefront of high-temperature processing technology.
Post time: Nov-22-2024